在工业热交换领域,缠绕管换热器正凭借其不断革新的技术,成为众多行业实现高效生产、节能减排的核心装备。其结构设计和性能表现,为复杂工况下的热交换需求提供了理想解决方案。
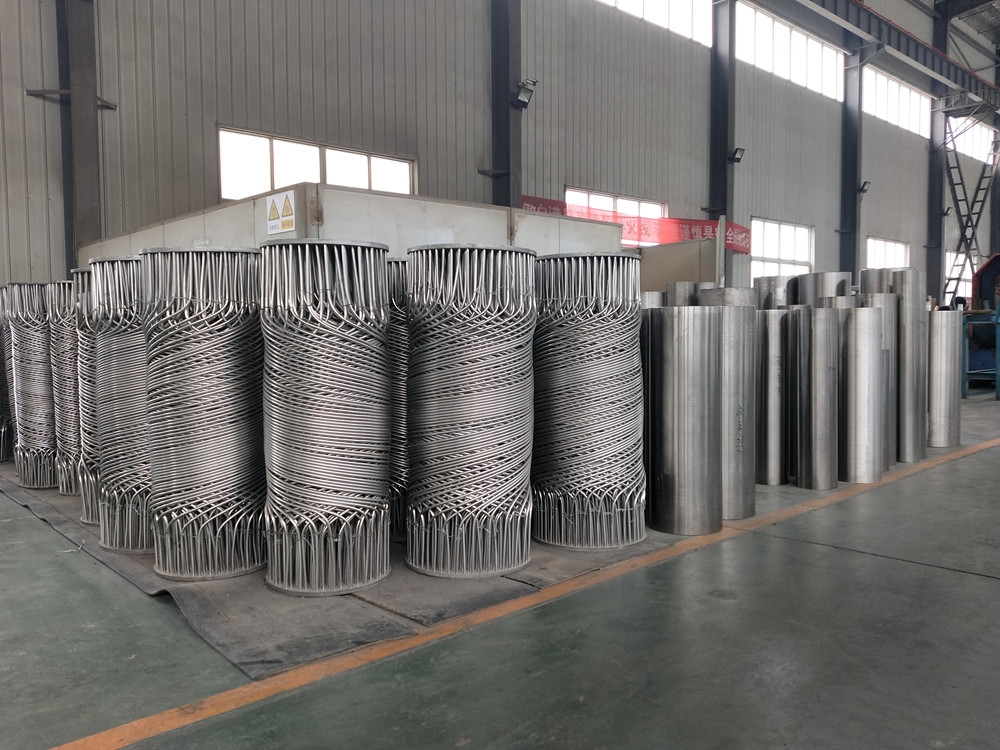
缠绕管换热器的技术原理基于其精巧的螺旋缠绕管束结构。相邻两层螺旋状传热管以相反方向紧密缠绕在中心筒体上,通过定距件精确保持管间距,从而构建出复杂且高效的三维流道。这种设计带来了一系列的技术特性。
多股流体同步换热是其显著优势之一。单台缠绕管换热器能够同时处理多股不同的流体,这就如同一个高效的交通枢纽,能同时疏导多路车流,极大地简化了整个热交换系统的布局,减少了设备数量和占地面积,降低了系统的复杂性和投资成本。在一些大型化工联合装置中,多种反应物料和冷却介质需要同时进行热交换,缠绕管换热器能够有条不紊地完成任务,确保各工艺环节的顺利进行。
强化湍流效应是提升传热效率的关键因素。当流体在螺旋通道内流动时,会自然形成二次环流,这种环流就像在平静的水流中制造出湍急的漩涡,使流体的流动状态变得更加复杂和活跃。流体与管壁之间的热量传递不再局限于传统的层流方式,而是在强烈的湍流作用下,热边界层被不断破坏和更新,传热系数得到显著提升。实验数据表明,缠绕管换热器的传热系数最高可达 14000W/(㎡?℃),相较于传统列管式换热器,换热效率提升了 30% - 50%,为工业生产中的热量回收和利用提供了强大的技术支持。
自补偿热应力特性使缠绕管换热器能够轻松应对大温差工况。由于管束两端的自由弯曲段可根据温度变化自行收缩或扩张,就像具有弹性的弹簧,能够有效地吸收因温度剧烈变化而产生的热应力,避免了应力集中导致的设备损坏。在一些高温高压的化工反应过程中,缠绕管换热器凭借这一特性,能够在如此苛刻的条件下稳定运行,设备寿命可延长至 30 - 40 年,大大减少了设备的更换频率和维护成本。
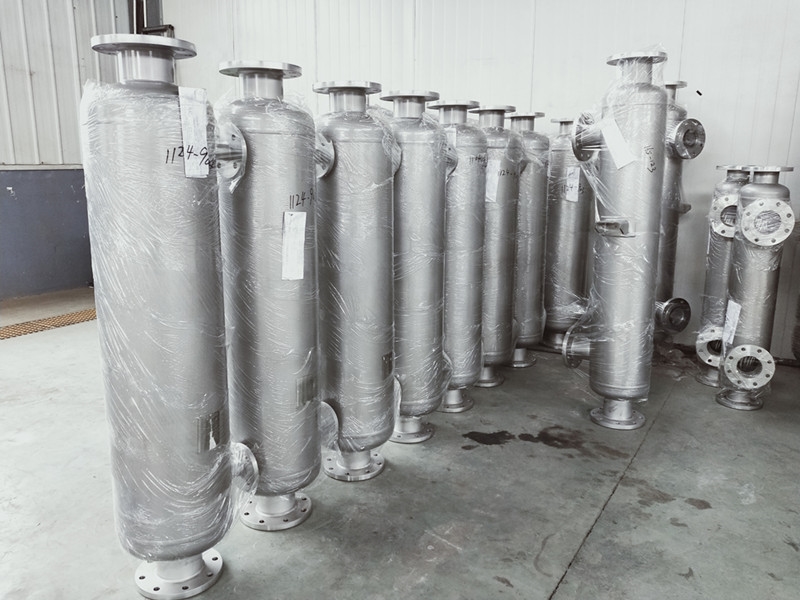
模块化灵活设计也是缠绕管换热器的一大亮点。它支持单根或多根组焊绕制,可根据不同的工艺需求和场地条件进行定制化设计。无论是小型工厂的紧凑生产线,还是大型工业项目的大规模热交换需求,都能通过模块化组装技术,快速、灵活地搭建出合适的换热系统,并且在后期需要扩容或改造时,能够方便地进行在线调整,某化工厂通过增加缠绕层数,轻松实现了换热能力提升 30%,且无需停机,极大地提高了生产的连续性和灵活性。
缠绕管换热器在核心优势方面表现得极为突出。在传热效率上,其性能令人瞩目。螺旋结构带来的强化传热效果,使得在相同的时间和空间内,能够传递更多的热量。在蒸汽冷凝工况下,冷凝效率高达 98%,显热回收率超 90%,这意味着大量的热能被充分回收利用,减少了能源的浪费,为企业降低了生产成本。
在适应性方面,缠绕管换热器堪称 “全能选手”。它能够耐受高达 20MPa 的高压,以及从 - 196℃的极低温到 800℃的高温,这种宽广的温度和压力适应范围,使其能够在各种工况下稳定运行。无论是在深海油气开采的高压低温环境,还是在高温冶炼的工业熔炉旁,都能找到缠绕管换热器可靠工作的身影。同时,它对介质的兼容性也非常广泛,可处理多相流以及含有固体颗粒、高黏度等复杂介质,在化工、石油、电力等行业的复杂工艺流程中发挥着关键作用。例如,在处理含 5% 固体颗粒的介质时,缠绕管换热器的压降仅为传统管壳式的 1/3,展现出了强大的抗污堵能力。
结构紧凑轻量化也是缠绕管换热器的一大特点。通过螺旋缠绕管束设计,其单位体积换热面积较传统设备提升了 60%,在实现高效换热的同时,占地面积减少了 40%。这一优势在土地资源紧张、空间有限的场所,如城市中的热电厂、海上石油钻井平台等,显得尤为重要。同时,全焊接结构采用耐腐蚀合金材料,不仅保证了设备的强度,还降低了整体重量,便于设备的安装和维护。